Wet sand making
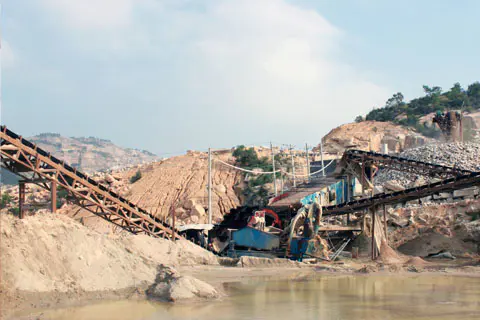
Результат проектирования
According to customer needs
Материал
Hard rock such as granite, diorite, basalt, conglomerate, sandstone, limestone, argillaceous limestone, dolomite, gneiss, quartzite, marble, slate, etc Soft rock such as tuff, nagelfluh, agrillaceous shale, argillaceous conglomerate, marl, mudstone, etc.
Заявление
It is suitable for applications in hydropower, highway, urban construction; the particle size can be combined and graded according to the different requirements of clients.
Оборудование
Vibrating feeder, vertical shaft impact crusher, vibrating screen, sand washer, fine sand collecting system, etc.
Introduction of wet sand making
Because we usually process stone materials, due to violent collisions and the stone material itself has a certain soil content, it will cause a certain amount of stone powder and mud powder in the manufactured sand. Mud powder has a serious impact on the quality of sand. Although the presence of stone powder can make up for the large gap caused by artificial sand in the concrete, but the configuration of concrete requires a large amount of water. Therefore, in order to solve the problem of powder content of manufactured sand, a sand washing machine is usually equipped in the manufactured sand production line, and then the mud powder in the sand is removed to achieve the standard of building sand. This is the wet sand production line.
The wet sand making production line is composed of vibrating feeder, jaw crusher, impact crusher or cone crusher, sand maker, sand washer, fine sand collecting system, vibrating screen and belt conveyor. According to different process requirements, various types of equipment are combined to meet different process requirements of customers.
Basic process introduction of Wet sand making plant
In the process of SANME wet sand making, new sand making machine has replaced the rod mill with high running cost, which greatly improve the reliability of artificial sand production, and ensure the quality of product.
The process is specifically designed for the material less than 40mm ( material will be primarily and secondarily crushed by jaw crusher, cone crusher, impact crusher, etc to the size less than 40mm ), vertical shaft impact crusher ( sand making machine ) is used in the configuration of production line, this crusher is the new type sand maker of SANME, which has the features of high crushing efficiency ( with the function of fine crushing and coarse grinding ), simple structure, easy installation and maintenance, low operation cost and excellent particle size ( cubic shape, low content of needle-like particles ).
Aggregate with size of 0-40mm will be conveyed by electromagnetic feeder and belt conveyor to vertical shaft impact crusher for crushing, the crushed material will be conveyed to vibrating screen for screening, the material with size larger than 5mm will be conveyed back to sand maker for crushing to achieve a closed circuit.
The material with size less than 5mm will be conveyed to sand washer for cleaning, the cleaned material will be conveyed by belt conveyor to final product pile. In order to ensure the fineness module and sand grading, the sand washing water will be recycled by fine sand collection system to collect the fine sand with size less than 0.16mm.
Flow chart of Wet sand making plant
Features of SANME wet sand making process
1. The design of process is scientific and reasonable, which effectively ensure the quality and output of manufactured sand.
2. It is capable of crushing middle and high as well as extra high hardness material.
3. High automation minimize the cost of human resource.
4. Good sand grading, adjustable fineness module.
5. Low running noise level, less dust pollution.
Техническое описание:
1. Этот процесс разработан в соответствии с параметрами, предоставленными заказчиком. Эта блок-схема предназначена только для справки.
2. Фактическая конструкция должна быть скорректирована в соответствии с местностью.
3. Содержание бурового раствора в материале не может превышать 10%, и содержание бурового раствора будет иметь важное значение для производительности, оборудования и процесса.
4. SANME может предоставить планы технологических процессов и техническую поддержку в соответствии с фактическими требованиями клиентов, а также может разработать нестандартные вспомогательные компоненты в соответствии с фактическими условиями установки клиентов.