Granite Aggregates Processing
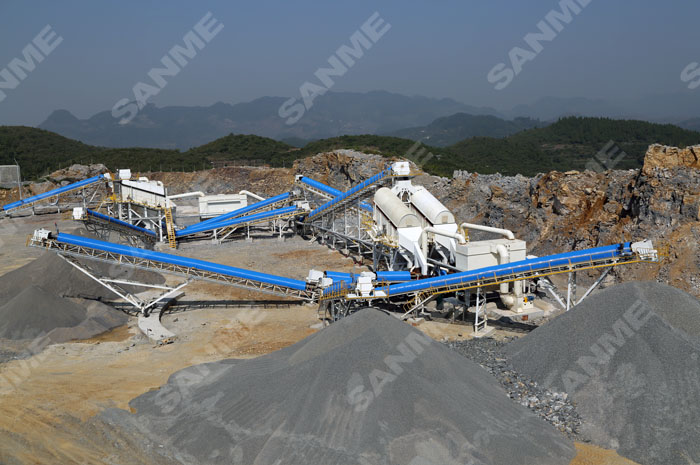
Результат проектирования
According to customer needs
Материал
It is suitable for primary, secondary and fine crushing of hard rock materials, such as basalt, granite, orthoclase, gabbro, diabase, diorite, peridotite, andesite, rhyolite, etc.
Заявление
It is suitable for application in hydropower, highway and urban construction, etc.
Оборудование
Jaw crusher, hydraulic cone crusher, sand maker, vibrating feeder, vibrating screen, belt conveyor.
Introduction of Granite
Granite is uniform in structure, rigid in texture and beautiful in color. It is a kind of high-quality durable aggregate and considered the king of stones. In building industry, granite can be everywhere from roof to floor. Being crushed, it can be used to produce cement and filling material. It is difficult for granite to weathering and its appearance and color can keep for over a century. Apart from being used as decorative building material and floor of hall, it is the first choice of open-air sculptures. Because granite is rare, it can add values of buildings whose floors are made from granite. Moreover, the natural countertop can tolerate heat so it is often taken priority among various building materials.
Basic process of granite crushing production plant
The granite crushing production line is divided into three stages: coarse crushing, medium fine crushing and screening.
The first stage: coarse crushing
The granite stone blasted from the mountain is fed uniformly by the vibrating feeder through the silo and transported to the jaw crusher for coarse crushing.
The second stage: medium and fine crushing
The coarsely crushed materials are screened by vibrating screen and then conveyed by belt conveyor to cone crusher for medium and fine crushing.
The third stage: screening
The medium and finely crushed stones are conveyed to the vibrating screen through a belt conveyor to separate stones of different specifications. The stones that meet the requirements of the customer's particle size are conveyed to the finished product pile through the belt conveyor. The impact crusher crushes again, forming a closed circuit cycle.
Flow chart of granite crushing production plant
Basic process of granite sand making plant
The granite sand making process is divided into four stages: coarse crushing, medium fine crushing, sand making and screening.
The first stage: coarse crushing
The granite stone blasted from the mountain is fed uniformly by the vibrating feeder through the silo and transported to the jaw crusher for coarse crushing.
The second stage: medium fine crushing
The coarsely crushed materials are screened by vibrating screen and then conveyed by belt conveyor to cone crusher for medium crushing. The crushed stones are conveyed to the vibrating screen through a belt conveyor to sieve out different specifications of stones. The stones that meet the requirements of the customer's particle size are conveyed to the finished product pile through the belt conveyor. The cone crusher crushes again, forming a closed circuit cycle.
The third stage: sand making
The crushed material is larger than the size of the two-layer screen, and the stone is conveyed to the sand maker machine through the belt conveyor for fine crushing and shaping.
The fourth stage: screening
The finely crushed and reshaped materials are screened by vibrating screen for coarse sand, medium sand and fine sand.
Note: For the sand powder with strict requirements, a sand washing machine can be added behind the fine sand. The waste water discharged from the sand washing machine can be recovered by the fine sand recycling device. On the one hand, it can reduce environmental pollution, and on the other hand, it can increase sand production.
Flow chart of granite sand making plant
Техническое описание:
1. Этот процесс разработан в соответствии с параметрами, предоставленными заказчиком. Эта блок-схема предназначена только для справки.
2. Фактическая конструкция должна быть скорректирована в соответствии с местностью.
3. Содержание бурового раствора в материале не может превышать 10%, и содержание бурового раствора будет иметь важное значение для производительности, оборудования и процесса.
4. SANME может предоставить планы технологических процессов и техническую поддержку в соответствии с фактическими требованиями клиентов, а также может разработать нестандартные вспомогательные компоненты в соответствии с фактическими условиями установки клиентов.